Providing Repair Solutions And Enhancing Products
Pressure
Vessels
Structural
Fabrications
Setting The Standard
Heartland Repair & Coatings (HRC) is an energy service company specializing in the design and fabrication of pressure vessels, processes piping and general fabrication. HRC is an accredited ASME Section VIII Div. 1 code facility holding both “U” and “R” stamps. HRC utilizes high pressure cold spray technology to provide protective coatings to enhance products for a variety of energy sector applications. The Team at Heartland Repair & Coatings sets the standard for quality, on time fabrication and high pressure cold spray applications. We are committed to nothing less then exceptional services and top-quality products for our customers.
Superior Repair Services
Heartland Repair & Coatings is an energy service company that specializes with ASME code work in vessels and piping with the ability to enhance products with cold spray for the energy sector.
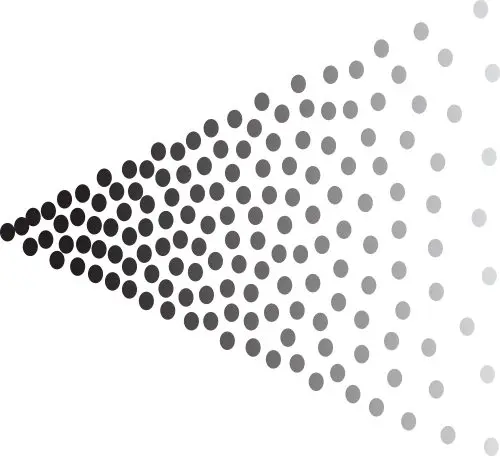
High Pressure Cold Spray
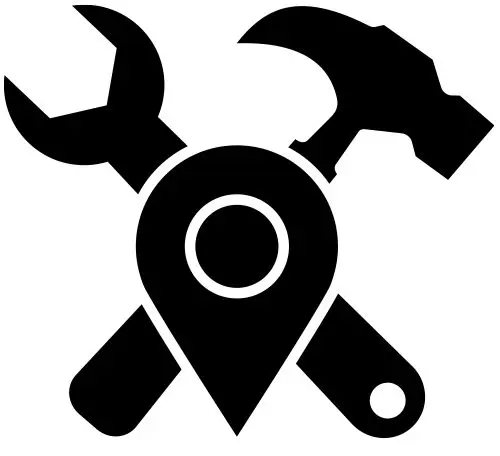
Mobile Services
Patented Pipe Repair
RRL Patented Pipe Repair
Utilizing the VRC Metal Systems Cold Spray Method, completely fill the defect in the pipe to a level beyond the original thickness.
Use of a disc grinder will smooth out the peaks and valleys formed during the void filling process. This will allow for a uniform surface to transfer the load in the pipe uniformly to the composite.
Mix the Anti-Corrosion epoxy uniformly. Apply the epoxy over the entire area to be wrapped by the composite. Ensure that it is applied to the required thickness and goes slightly beyond the width of the wrap that follows. Spray water before and during the wrapping process to activate the resin inside the carbon fiber composite.
Center the repaired area under the composite and wrap the carbon fiber roll to the specified number of layers. Immediately after wrapping the composite, utilize compression film to press all of the layers together and to protect the composite while it cures. Be sure to perforate the compression film to allow excess water and resin to escape while the composite cures. When the resin hardens and is dry to touch, the compression film can be removed and the pipe is ready to be backfilled.
Patented Pipe Repair
RRL Patented Pipe Repair
Utilizing the VRC Metal Systems Cold Spray Method, completely fill the defect in the pipe to a level beyond the original thickness.
Use of a disc grinder will smooth out the peaks and valleys formed during the void filling process. This will allow for a uniform surface to transfer the load in the pipe uniformly to the composite.
Mix the Anti-Corrosion epoxy uniformly. Apply the epoxy over the entire area to be wrapped by the composite. Ensure that it is applied to the required thickness and goes slightly beyond the width of the wrap that follows. Spray water before and during the wrapping process to activate the resin inside the carbon fiber composite. Center the repaired area under the composite and wrap the carbon fiber roll to the specified number of layers. Immediately after wrapping the composite, utilize compression film to press all of the layers together and to protect the composite while it cures. Be sure to perforate the compression film to allow excess water and resin to escape while the composite cures. When the resin hardens and is dry to touch, the compression film can be removed and the pipe is ready to be backfilled.
Industries Served
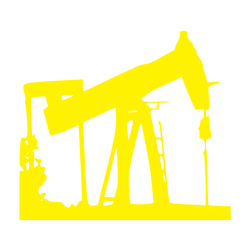
Oil & Gas
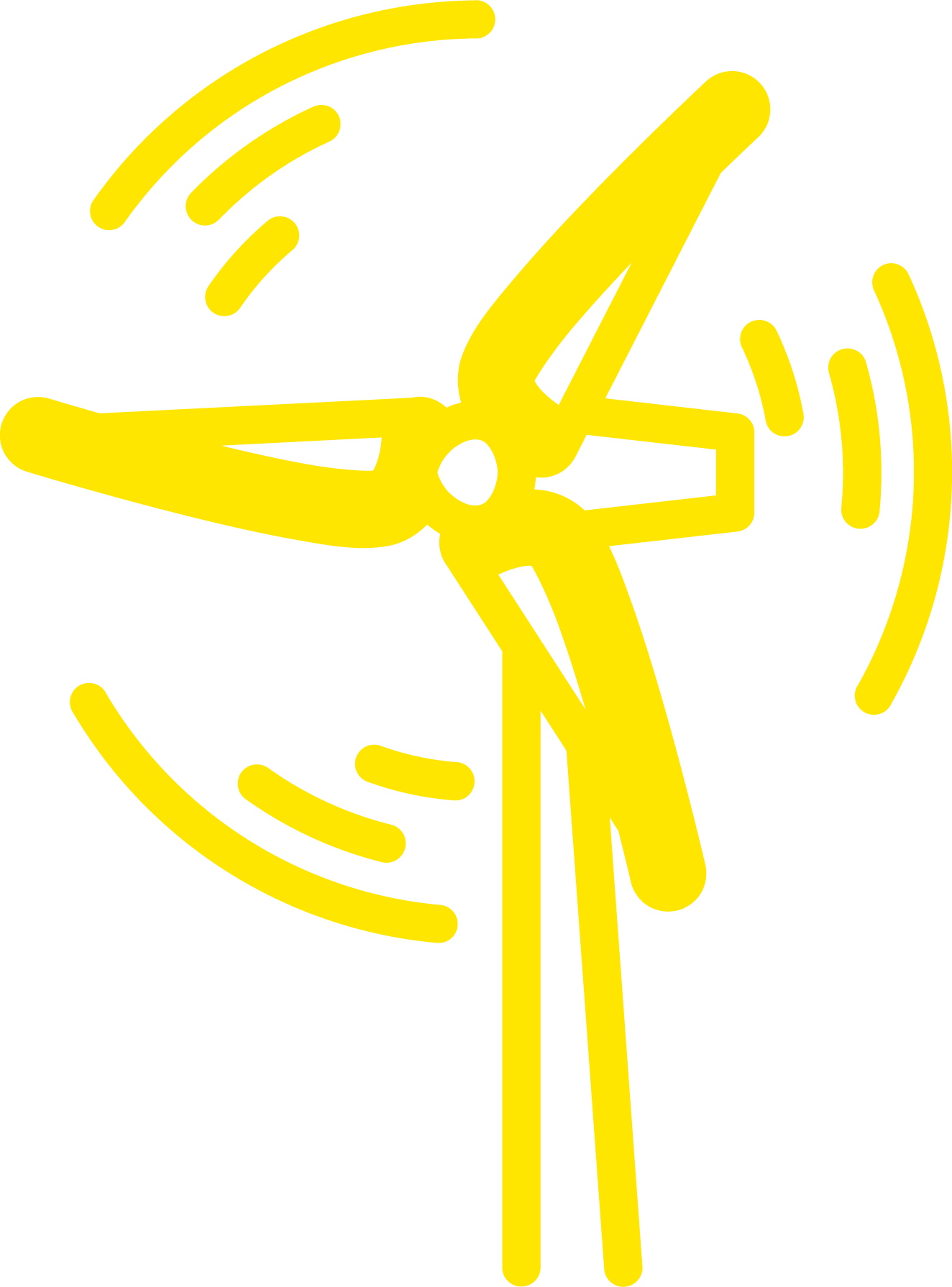
Renewable Energy
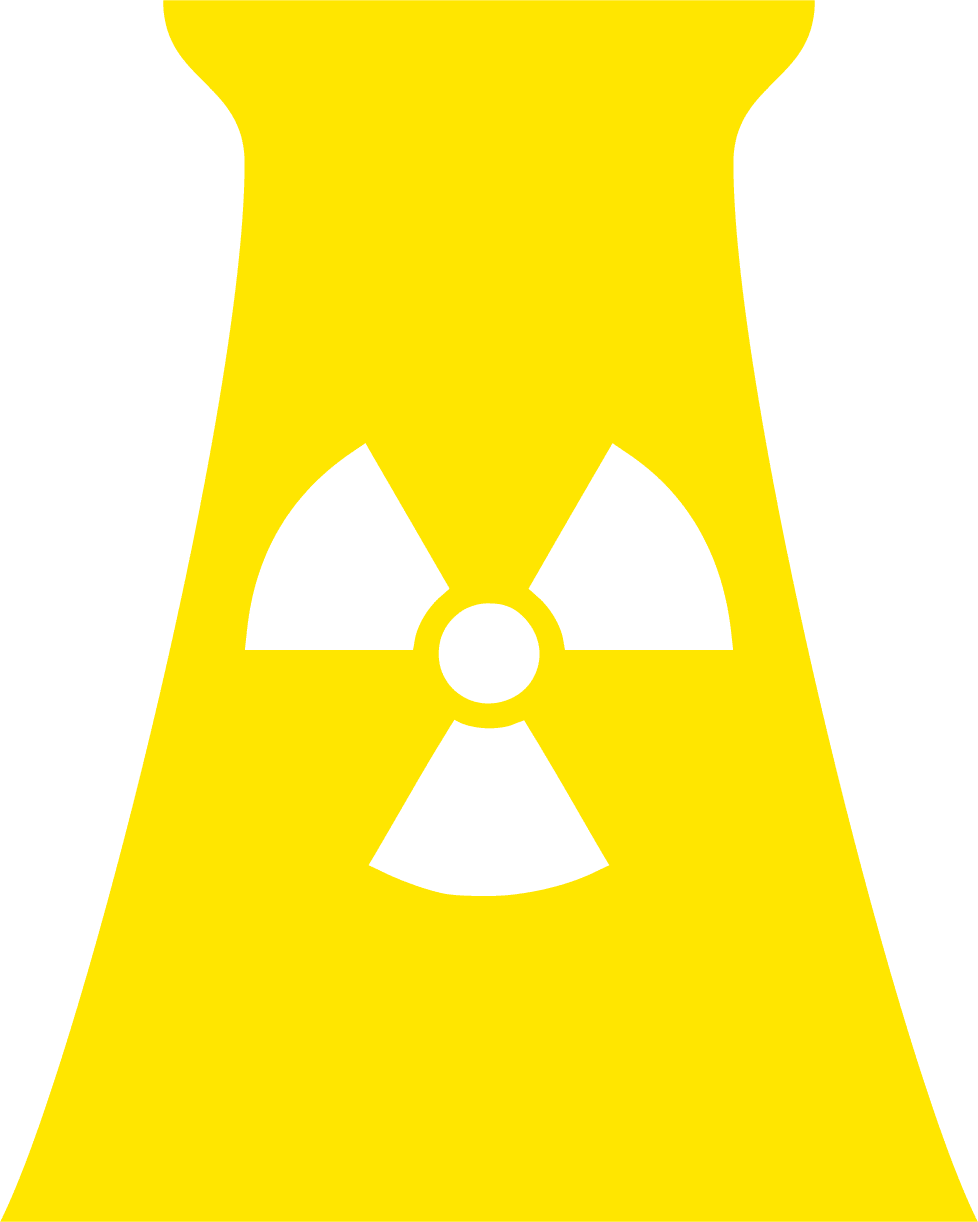
Nuclear Power
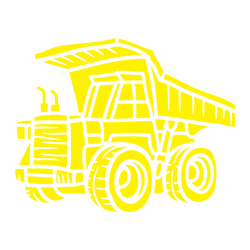
Mining
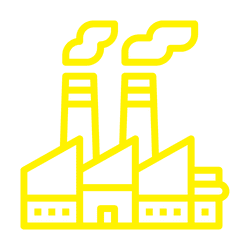
Heavy Industrial
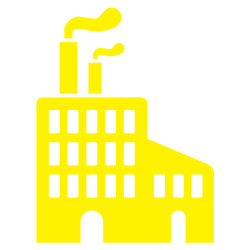
Petrochemical
Certifications
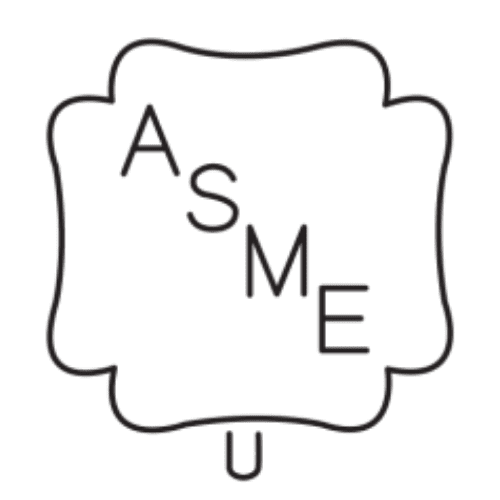
ASME Certified; U Stamp
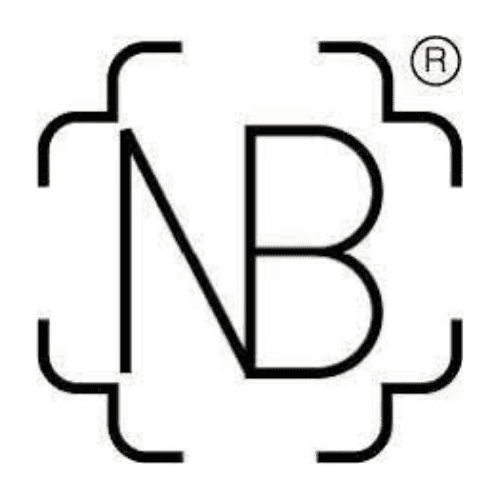
National Board of Boiler & Pressure Vessel Inspectors Certified; NB Stamp
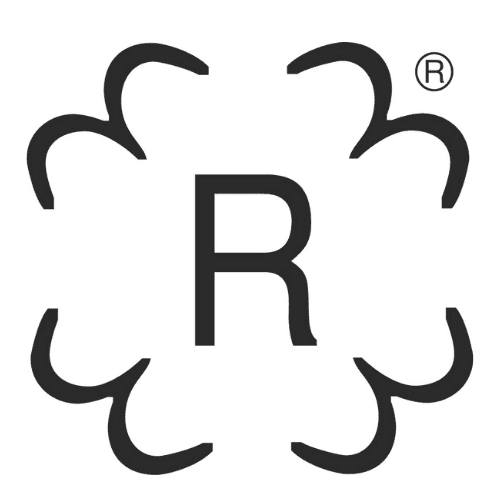