Ensuring Safety & Compliance: The Inspection & Maintenance of Oil and Gas Pressure Vessels
Oil and gas production facilities rely heavily on the use of pressure vessels for daily operations. Pressure vessel are extensively utilized in the oil and gas industry and serve multiple purposes, such as separating crude oil from natural gas, storing crude oil, and facilitating petroleum transport. When pressure vessels are used to store and process flammable or combustible liquids, the Occupational Safety and Health Administration (OSHA), American Society of Mechanical Engineers (ASME), and the American Petroleum Institute (API) all recognize that safe practice or good engineering practices must be followed in accordance with adopted pressure vessel codes and regulations.
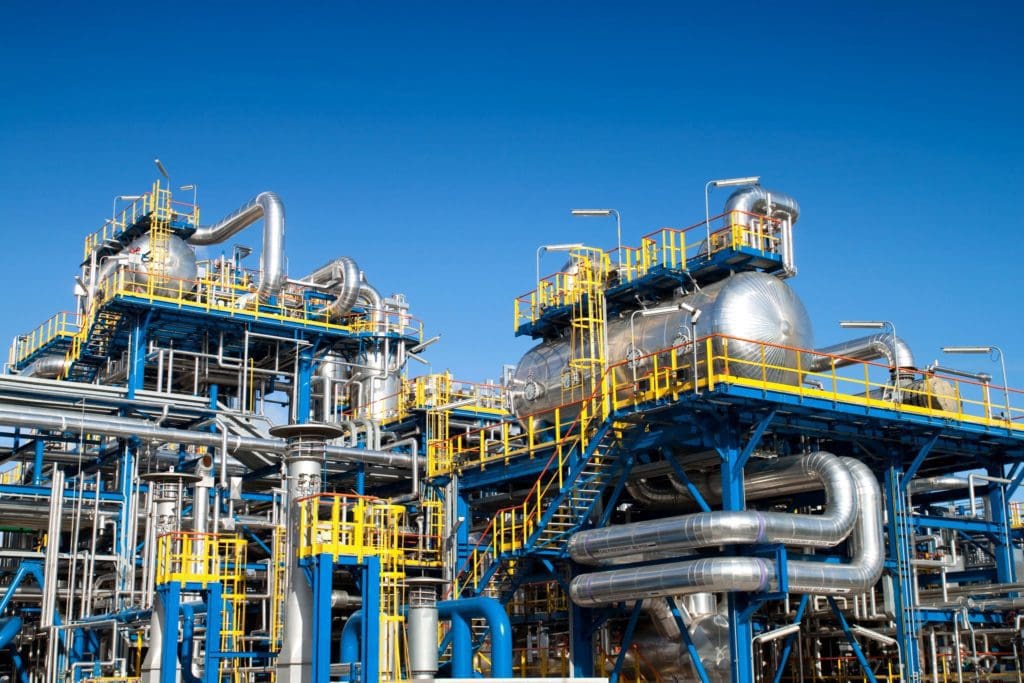
Pressure vessels can represent a serious safety hazard as a result of the failure of pressure vessels used for oil and gas production purposes, which is why safeguards must be put in place to protect the lives of all employees present at oil and gas processing facilities. Regular inspection and maintenance of these facilities is necessary to ensure oil and gas production operations stay safe, efficient, and productive.
To illustrate the importance of pressure vessel safety regulations, it is necessary to look at the potential threats that safety pressure vessels present to oil and gas workers on a daily basis, while also looking at some of the different regulations that seek to avoid safety hazards and catastrophic failure of pressure vessels. With these examples in mind, it will become abundantly clear as to why pressure vessel construction and maintenance requires stringent safety standards with regular inspections and routine maintenance
Potential hazards for pressure vessels in oil and gas production
Pressure vessels are critical components in oil and gas, petrochemicals, and more. While they are designed to withstand high pressures and temperatures, failures can occur due to various factors. Some potential safety issues and examples of catastrophic failures of pressure vessels include:
- Overpressure: When a pressure vessel is exposed to pressures beyond its design limits, it can lead to overpressure failure. This may result from process upsets, blocked outlets, or failure of pressure-relief devices. The vessel may rupture, causing a potentially hazardous release of the stored fluid or gas.
- Corrosion: Corrosion is a common issue that can weaken the structural integrity of pressure vessels over time. External corrosion from environmental factors or internal corrosion due to the stored material can cause thinning of the vessel walls and increase the risk of failure.
- Fatigue: Repeated cycles of pressure variation can lead to fatigue failure in pressure vessels. This is common in vessels subjected to frequent startups, shutdowns, and temperature fluctuations.
- Welding Defects: Poor welding practices or defects in welds can compromise the integrity of pressure vessels, leading to failures at the welded joints.
- Brittle Fracture: Exposure to low temperatures can make some materials more susceptible to brittle fracture. Sudden impacts or rapid temperature changes can trigger this type of failure.
- Material Defects: Inadequate material quality or flaws in the manufacturing process can result in pressure vessels having weak spots that are prone to failure.
- Erosion: In certain applications, such as in oil and gas pipelines, erosion caused by the high-velocity flow of fluids can wear away the inner surface of the vessel, leading to reduced thickness and potential failure.
- Fire Exposure: Pressure vessels located in fire-prone areas can be exposed to high temperatures, which may cause weakening and potential failure of the vessel.
Catastrophic Failure
The 2005 Buncefield Oil Depot Explosion
The Buncefield oil depot explosion in the UK in 2005 is an infamous example of a catastrophic failure of a large storage tank or storage vessel. A series of explosions occurred due to the overfilling of a storage tank, leading to the release of over 300 tons of petroleum, a massive fire and extensive property damage.¹
To prevent such incidents, pressure vessels must undergo regular inspections, maintenance, and compliance with safety standards. Proper risk assessments and mitigation strategies should be implemented to ensure the safe operation of pressure vessels and protect the surrounding environment and personnel.
American Petroleum Institute Pressure Vessel Industry Standards
The American Petroleum Institute is the only national trade association that represents all aspects of America’s oil and natural gas industry. The API was first formed in 1919 as a standards-setting organization. In its first 100 years, the API has developed more than 700 standards to enhance operational and environmental safety, efficiency, and sustainability. Here are some of the API’s adopted standards to ensure the proper operation and safety of oil and gas production pressure vessels:
API RP 74: Recommends practices and procedures for promoting and maintaining safe working conditions for personnel engaged in onshore oil and gas production operations, including special services.
API 12J: is an industry specification which covers among others the minimum requirements for the design and fabrication of oilfield type oil-gas-water separators used in the production of oil and/or gas. This specification contains many references to Code requirements such as construction, materials, testing, nameplate, stamping, etc.
API 12L: is an industry specification that includes the minimum requirements for vertical and horizontal emulsion treaters. These treaters are pressure vessels used in the production industry for separating oil-water emulsions and gas. The function of these treaters is to dehydrate or dewater the produced crude oil to a specified level. This specification also contains many references to Code requirements such as construction, materials, corrosion, testing, inspection, nameplate, etc.
API 510: Applies to among others, pressure vessels constructed in accordance with the API/ASME Code for Unfired Pressure Vessels for Petroleum Liquids and Gasses, Section VIII of the Code. API 510 states that in 1931, API and ASME created a joint committee to formulate and prepare a code for safe practices for pressure vessels in the petroleum industry. These safe practices include the design and construction of pressure vessels. That code was titled the API/ASME Code for Unfired Pressure Vessels for Petroleum Liquids and Gasses and was first published in 1934. API/ASME stated that they believed the Code actually applied to pressure vessels in most services.² ³
Regular Inspection and Maintenance of Oil and Gas Pressure Vessels
With great power comes great responsibility. The engineering processes that occur on a regular basis require the conversion of great amounts of energy for transportation of crude oil and its processing. With increased scrutiny on safety, efficiency, and sustainability, new technologies are constantly being developed to ensure safety standards are met. All types of pressure vessels, old and new, must be regularly inspected, maintained, and repaired to meet the standards required by the API, OSHA, and ASME.
Repairing Pressure Vessels with Heartland Repair & Coatings
Heartland Repair & Coatings (HRC) utilizes high pressure cold spray technology in addition to traditional heat welding to repair pressure vessels and provide protective coatings to enhance products for a variety of energy sector applications. From engineering, logistics, welding, nondestructive examination (NDE), hydro testing, and painting, the team at HRC will ensure your pressure vessel meets your engineering specifications while adhering to modern safety standards. Heartland Repair and Coatings is certified with the ASME National Board of Boiler & Pressure Vessel Inspectors. Learn more about our Heartland Repair Pressure Vessel Services today!
HRC Certifications
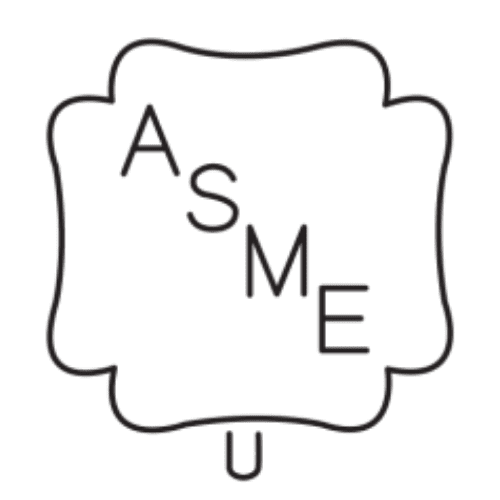
ASME Certified; U Stamp
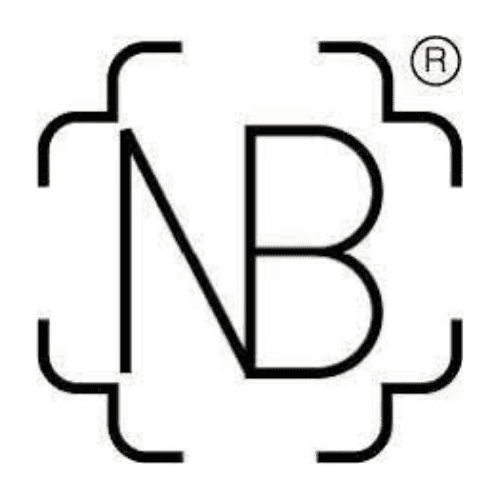
National Board of Boiler & Pressure Vessel Inspectors Certified; NB Stamp
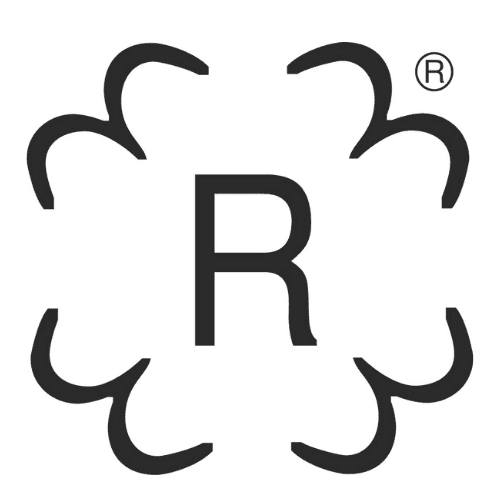
National Board of Boiler & Pressure Vessel Inspectors Certified; R Stamp
Sources
British Geological Survey 1998 – 2019 (c)UKRI http://www.bgs.ac.uk mailto:[email protected], “Analysis of the Buncefield Oil Depot Explosion 11 December 2005,” Buncefield Explosion Analysis, accessed August 16, 2023, http://www.earthquakes.bgs.ac.uk/research/events/buncefield_explosion.html#:~:text=The%20explosion%20was%20caused%20by,of%2043%20people%20were%20injured.
2. “Pressure Vessels Used at Oil and Gas Extraction/Production Facilities and Applicability of 29 CFR 1910.106: Occupational Safety and Health Administration,” Pressure vessels used at oil and gas extraction/production facilities and applicability of 29 CFR 1910.106 | Occupational Safety and Health Administration, accessed August 16, 2023, https://www.osha.gov/laws-regs/standardinterpretations/2006-07-17-0#:~:text=These%20treaters%20are%20pressure%20vessels,oil%20to%20a%20specified%20level.
3. “API Occupational Safety and Health Standards,” Energy API, accessed August 16, 2023, https://www.api.org/oil-and-natural-gas/health-and-safety/worker-and-worksite-safety-resources/api-osh-standards.