Building Pressure Vessels: What Are The Most Corrosion Resistant Alloys?
Improper selection of material is one of the leading causes of failures in pressure vessels. For this reason, selecting the proper materials and metals based on your intended use is imperative for success with your pressure vessel system. Choosing the wrong metal types can lead to a number of issues including, but not limited to, corrosion, poor performance, lower efficiency, reduced safety and catastrophic failure. Corrosion resistant alloys are necessary for an effective pressure vessel system.
Corrosion resistance is one of the biggest factors to take into consideration when determining which alloy to use in your pressure vessel. Corrosion resistance is “the capacity to hold the binding energy of a metal and withstand the deterioration and chemical breakdown that would otherwise occur when the material is exposed to such an environment.” (corrosionpedia.com) Basically, it is how well a material is able to prevent environmental deterioration by chemical or electro-chemical reactions. Given how many industries rely on pressure vessels, ensuring the proper level of corrosion resistance of the material is necessary for success.
You may be asking yourself, exactly what is a pressure vessel? Let’s look at that first.
What Are Pressure Vessels?
Pressure vessels are enclosed containers for liquids, vapors and gasses being held at pressure significantly higher or lower than ambient pressure. Pressure vessels are used throughout various industries such as oil and gas, chemical and food processing. Items such as reactors, flash drums and heat exchangers are just some examples of common pressure vessels.
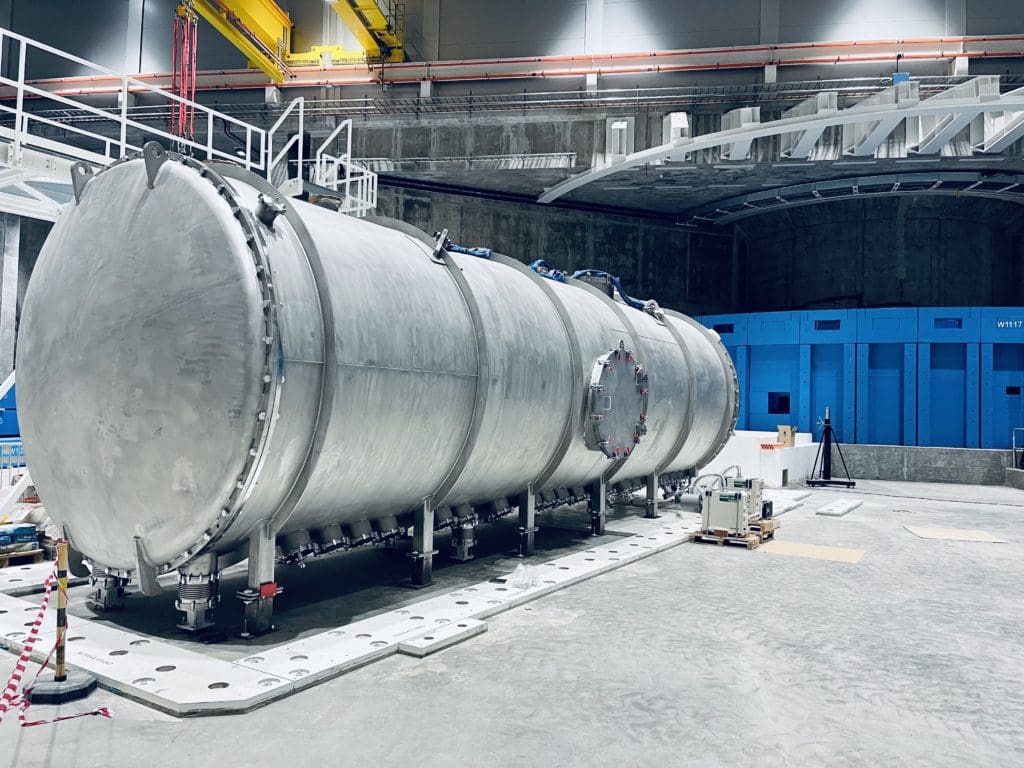
There are many standards and regulatory governing bodies when it comes to pressure vessels, but the ASME Boiler and Pressure Vessel Code (BPVC) is the most popular set of standards. The ASME BPVC is universally accepted standards that govern the design, construction, installation, testing, inspection and certification of pressure vessels, boilers and nuclear power plants.
All guidelines and divisions are in place to ensure not only the highest standard of products, but to also ensure maximum safety. This is also important when looking at the types of materials for your pressure vessels and their purposes.
Most Corrosion Resistant Alloys For Pressure Vessels
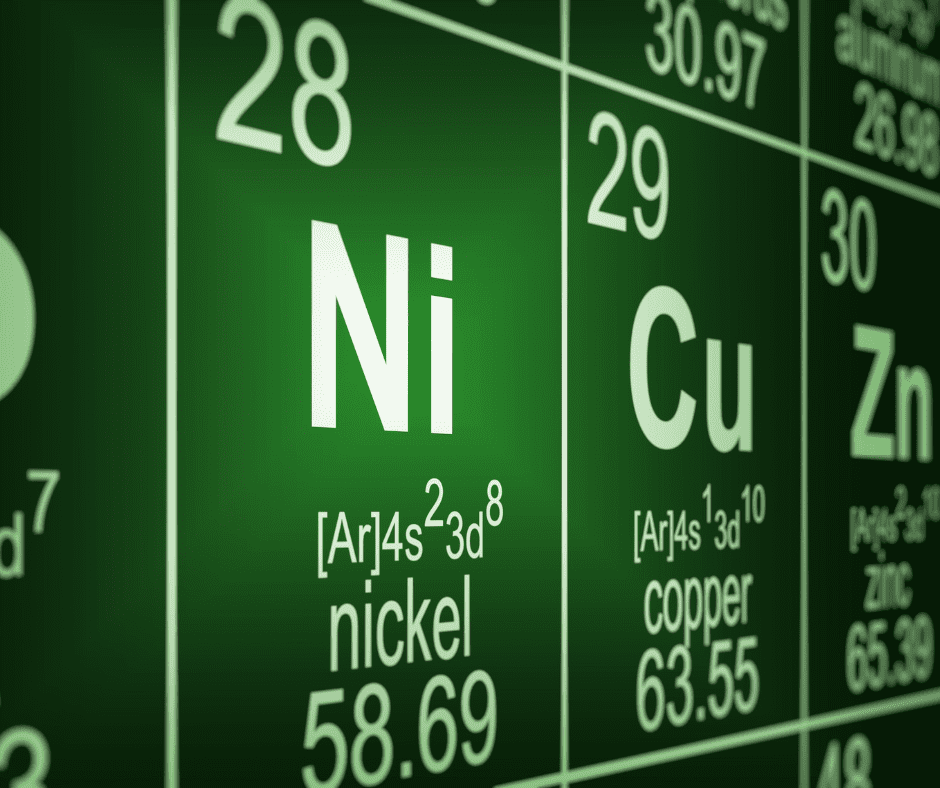
The most common materials used for constructing pressure vessels are Carbon Steel, Stainless Steel, Hastelloy, Nickel Alloys, Aluminum and Titanium. Each alloy brings their own set of benefits and drawbacks making each alloy a better choice than others in certain cases. Let’s take a look at each alloy’s corrosion resistance, starting from the least resistant; Carbon Steel.
Carbon Steel
Carbon Steel does not typically have enough chromium to form a chromium oxide layer similar to stainless steel. The lack of this layer allows oxygen to bond with the iron in carbon steel, creating iron oxide, or rust. Carbon steel is made from iron which is easy to corrupt due to the oxidizable iron. Because of its low corrosion resistance, carbon steel is not typically used when exposed to moisture, salt water, sulfuric acid or any other corrosive materials.
Aluminum
Aluminum is considered by many to be a top casting material due to its advantages over other metals. Aluminum alloy has ductility, high castability, high strength and good corrosion resistance. Aluminum’s corrosion resistance is created by an inert oxide film forming on the metal surface, creating a protective layer. However, this layer can give out and is prone to become unstable if placed in specific conditions. Aluminum corrosion most often occurs due to galvanization, which is where metals (two or more) are positioned for an electrical circuit. This process makes one metal stronger and the other metal, in this case aluminum, weaker. Galvanization is one of the leading causes of corrosion in aluminum. Aluminum corrosion can also occur due to extreme pH levels. Very high and low pH can break down the aluminum oxide coating, leaving the alloy completely open to corrosion. It is not the least corrosion resistant alloy available but it gets the job done in the right circumstances and still has its many benefits.
Stainless Steel
Stainless steel is considered one of the most corrosion resistant metals available (although not the best). The corrosion resistance of stainless steel is primarily due to the amount of chromium present which creates a chromium oxide layer to protect against corrosion. Unlike iron oxide, chromium oxide creates a thin layer that clings to the steel, acting as a protective barrier.
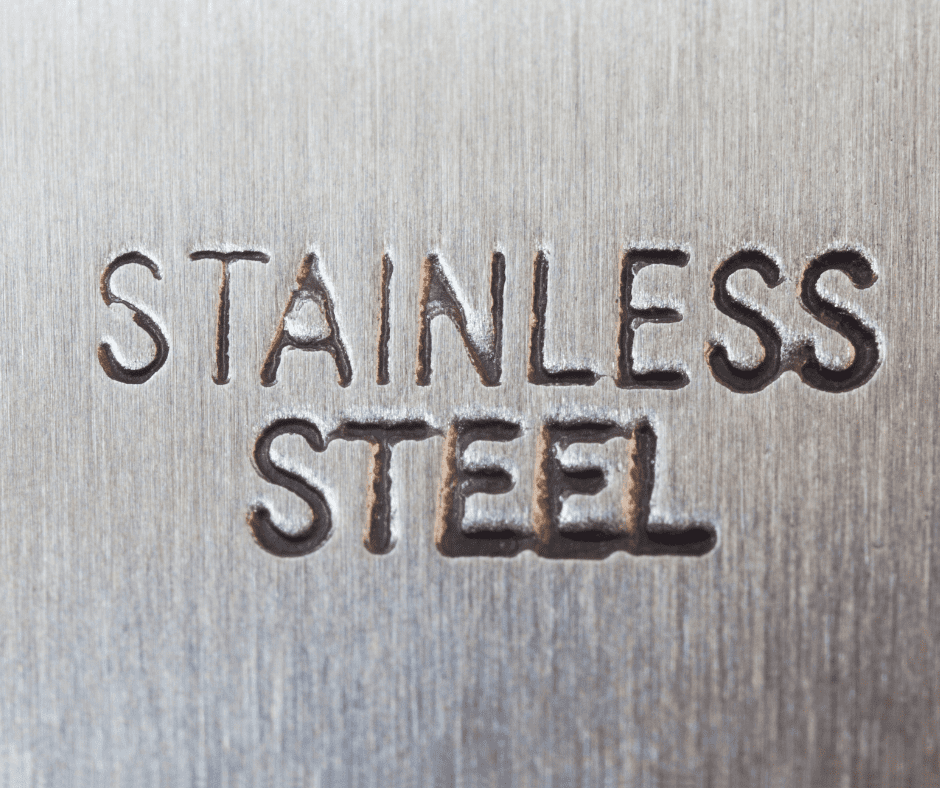
However, stainless steel can still rust when exposed to harmful chemicals, saline, grease, moisture or heat for prolonged periods of time. Stainless steel is a great option for most pressure vessels, but keep in mind that your specific use case may call for something with more corrosion resistance.
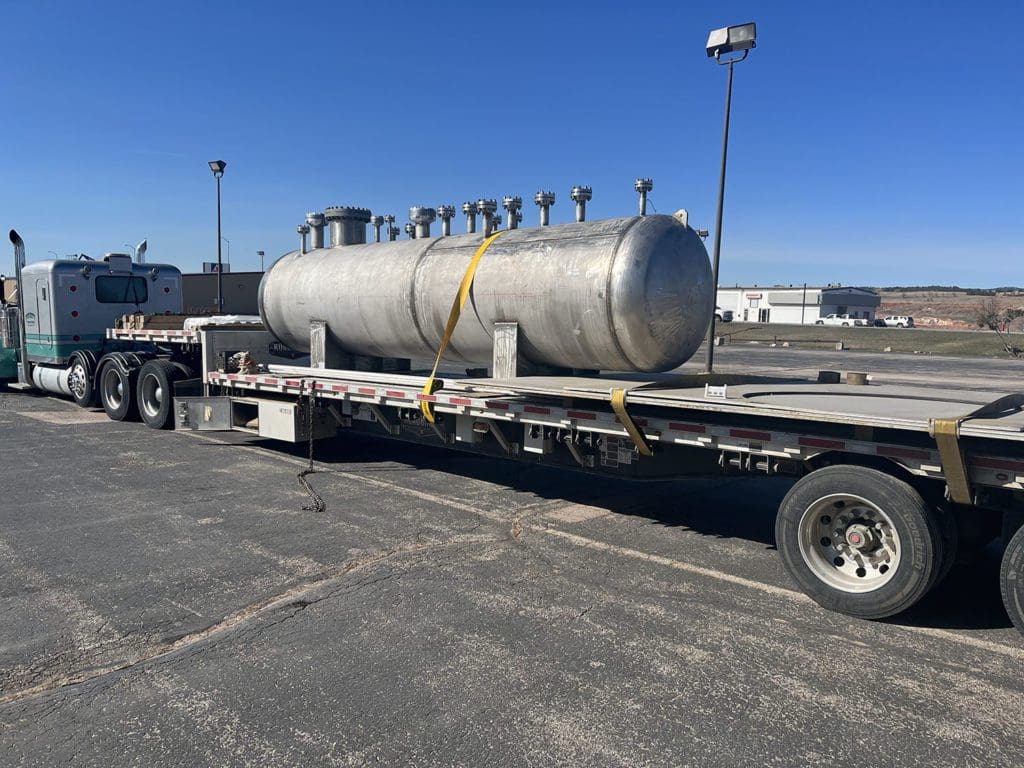
Nickel Alloys
Nickel and nickel alloys are highly resistant to corrosive environments, especially those that are too harsh for stainless steel. Nickel and nickel alloys make great materials for chemical processing and other industrial processing operations due to their corrosion resistance. Nickel boasts such great resistance because the standard reduction potential of nickel is more positive than iron, but less negative than copper.
Nickel alloys have great corrosion resistance and high temperature corrosion resistance to today’s chemical, petrochemical, marine, paper, agrochemical, oil and gas, energy conversion and many other corrosion issues in industrial environments. Nickel alloys make a great choice for pressure vessels but may not be the best choice for your specific application.
Titanium
Titanium is an oxide ore and is the 4th most abundant metallic element in the Earth’s crust. As a reactive material, Titanium shows amazing corrosion resistance in oxidizing acidic environments due to its passive oxide film. This film is significantly more protective than Stainless Steel and performs better in environments that cause pitting and crevice corrosion, such as seawater. Additionally, Titanium has a high resistance to steam and other caustic environments. Primarily having been used in Aerospace applications, Titanium is now finding itself being used across many industries and applications, including pressure vessel piping & tubing.
Conclusion
As we spoke earlier, choosing the proper material for your pressure vessel is imperative for success, as the wrong material is what causes most failures due to corrosion. Corrosion resistance should be one of the first attributes you look at when designing your pressure vessel. The metals and alloys we spoke about are all great options, but remember, each material brings their own unique properties thus their own benefits and drawbacks.
If you are not sure where to begin or how to start, contact Heartland Repair & Coatings today! We will help you from start to finish, helping you understand every step of the way. Contact us now!
Sources: